Composites
On Purdue Space Program Liquids I am leading the design-manufacture-test campaign for composites. We are making structural airframe sections, fins, a nosecone, and airframe panels, using oven cured prepreg fabric in a two piece vacuum bagged mold. The mold itself is tooling prepreg cured over a male mold of the part. We are also hand wrapping our engine in silica phenolic ablative with a carbon fiber / epoxy overwrap.
I am using Ansys ACP to design and simulate the strength of composite airframes. We will be running experimental tests to validate the accuracy of our simulations before making the final airframe.
I also made a fiberglass airframe from scratch for my L1 high power rocket. Check previous posts for manufacturing and testing and defects.
We are currently in the process of destructively testing scale carbon fiber airframes to characterize skin buckling failure with our manufacturing techniques/quality.
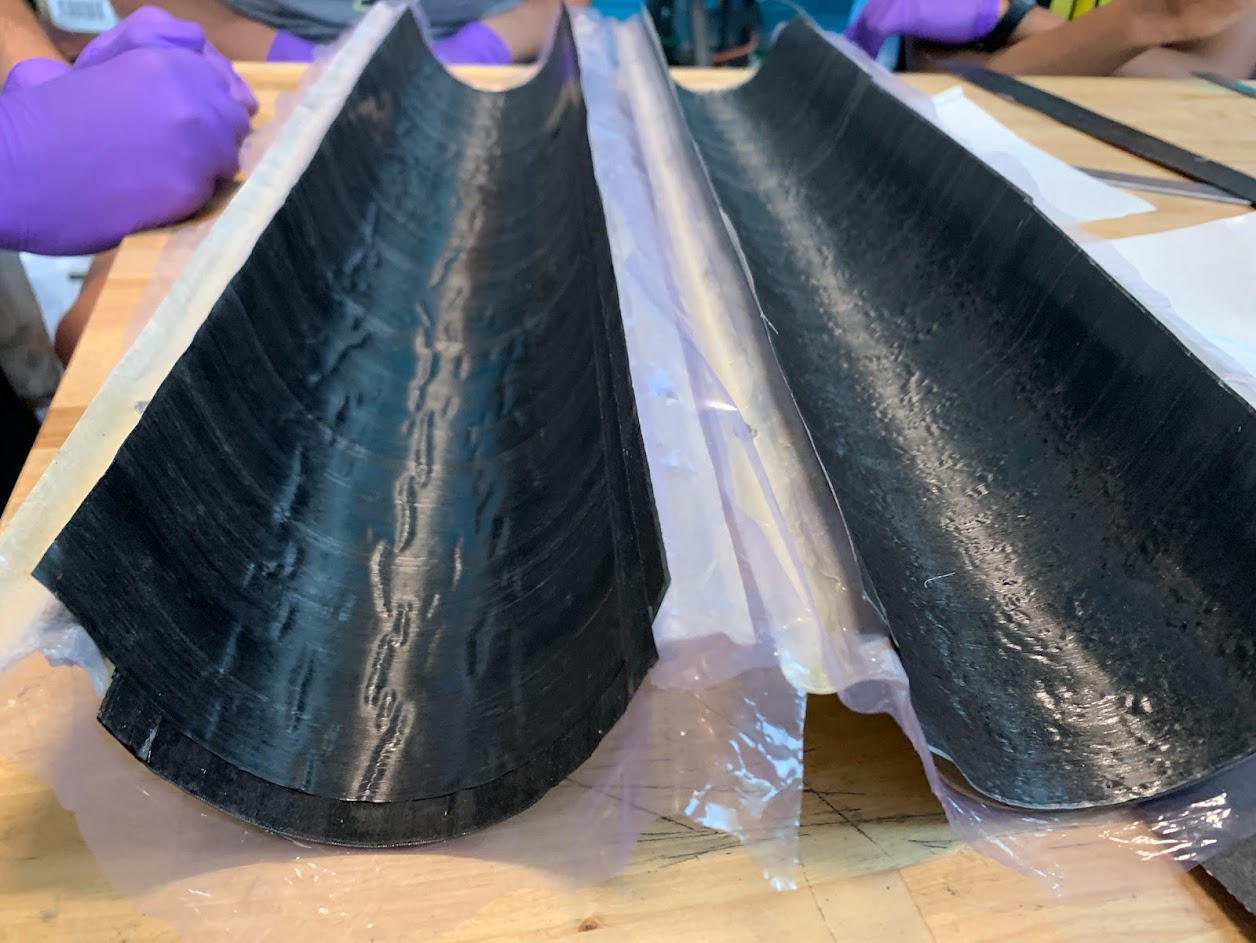

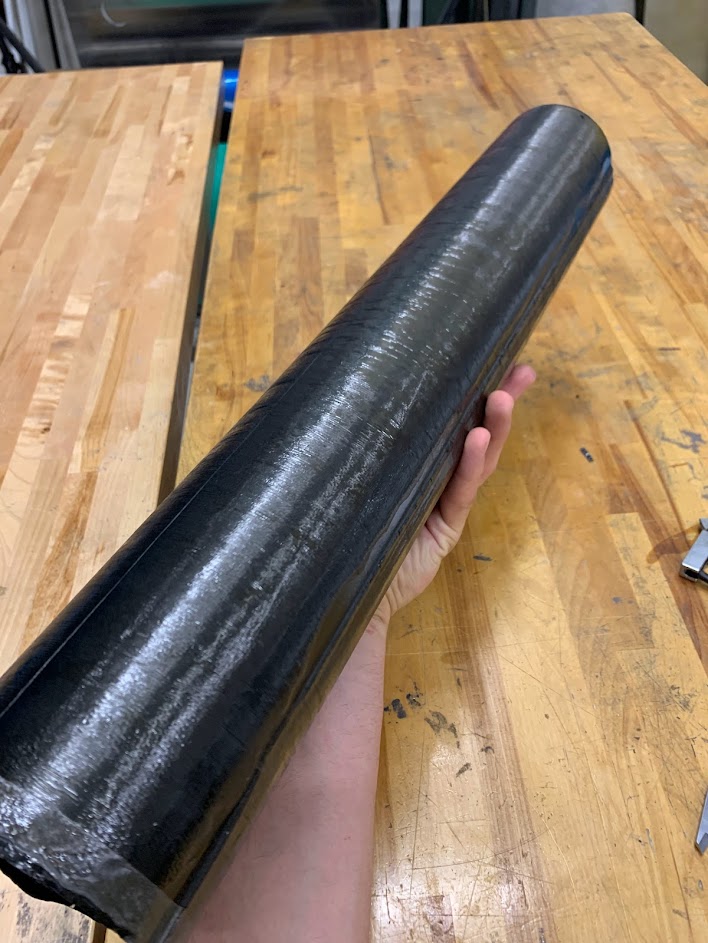
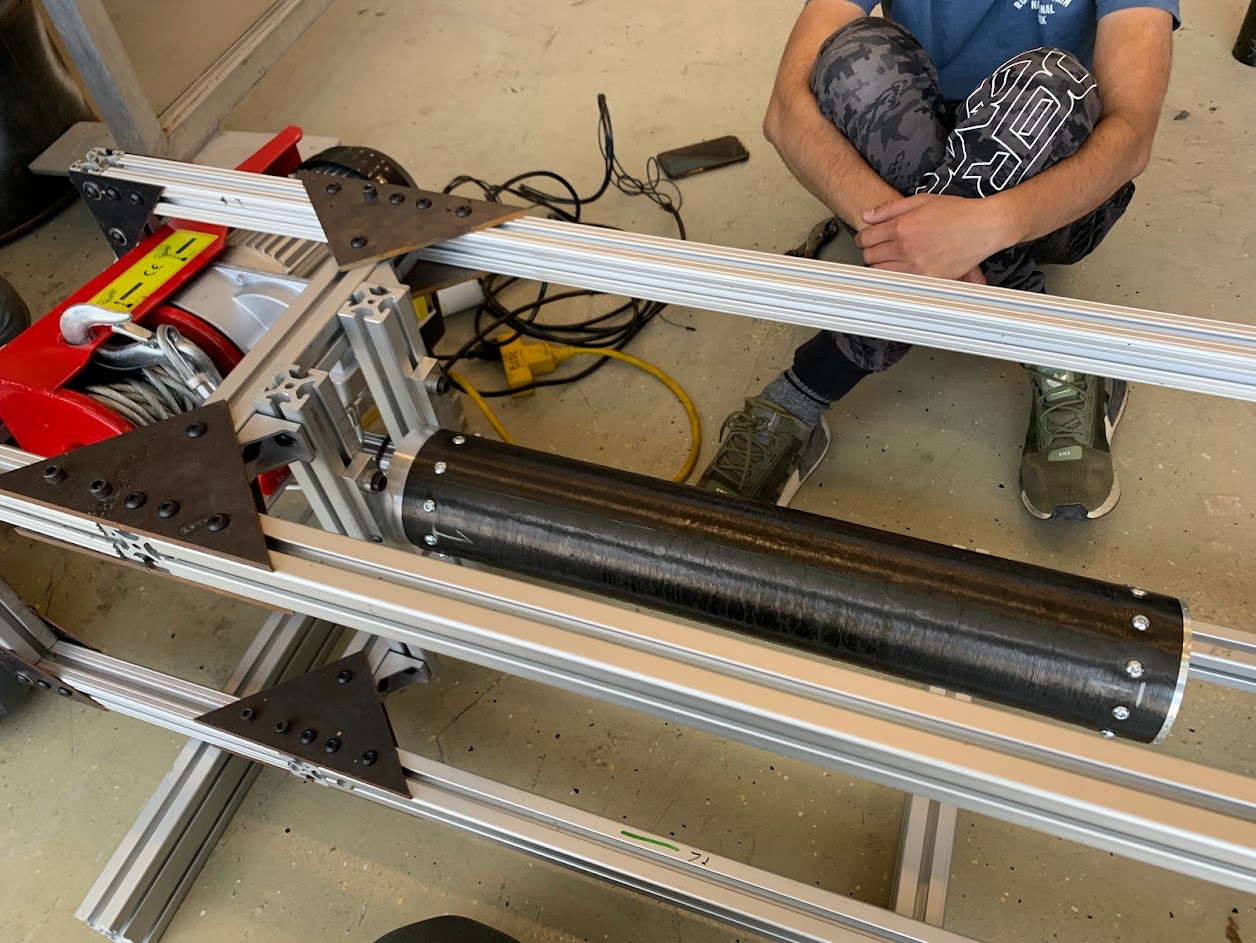
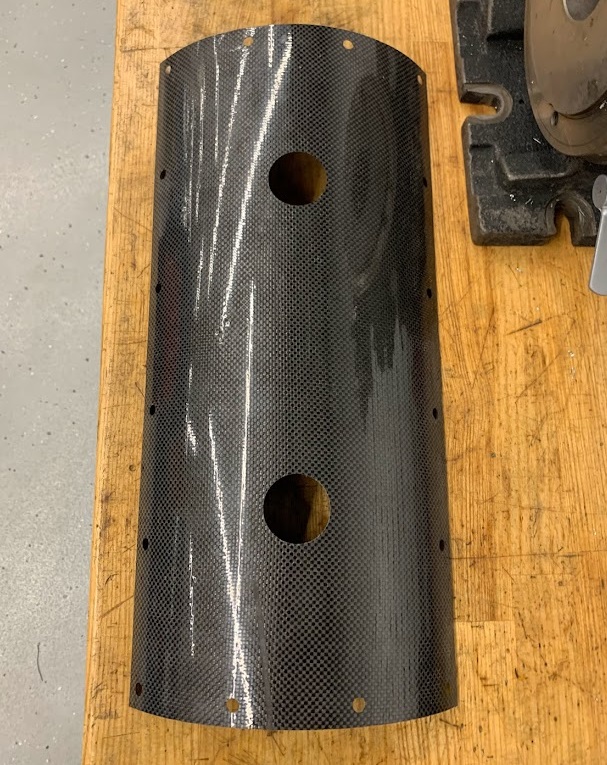
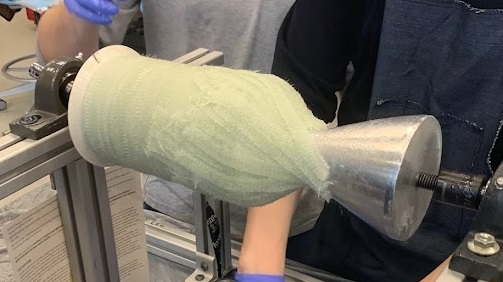
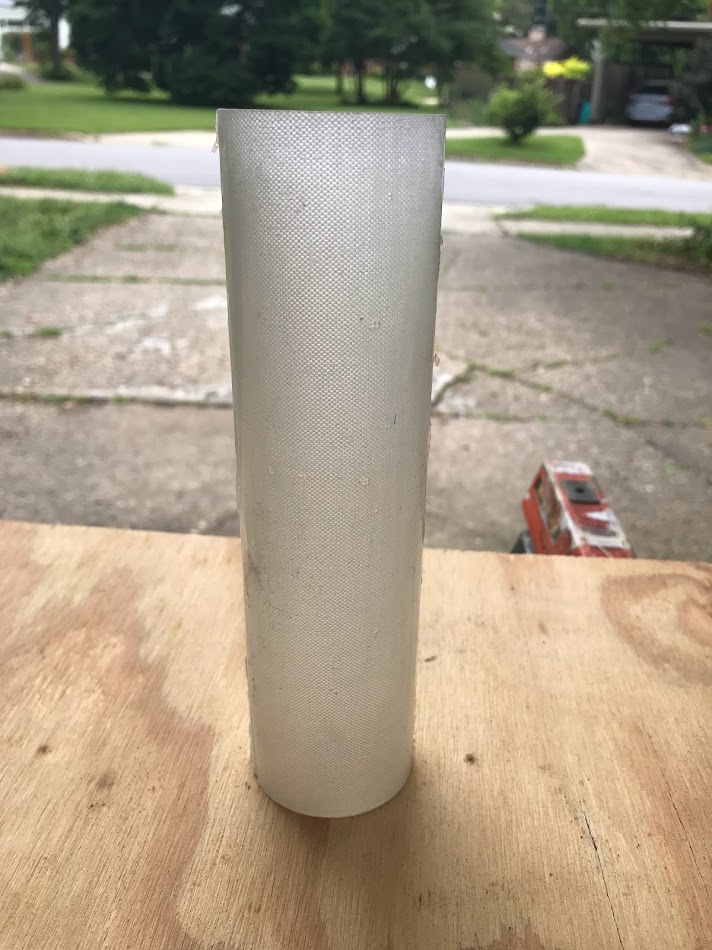